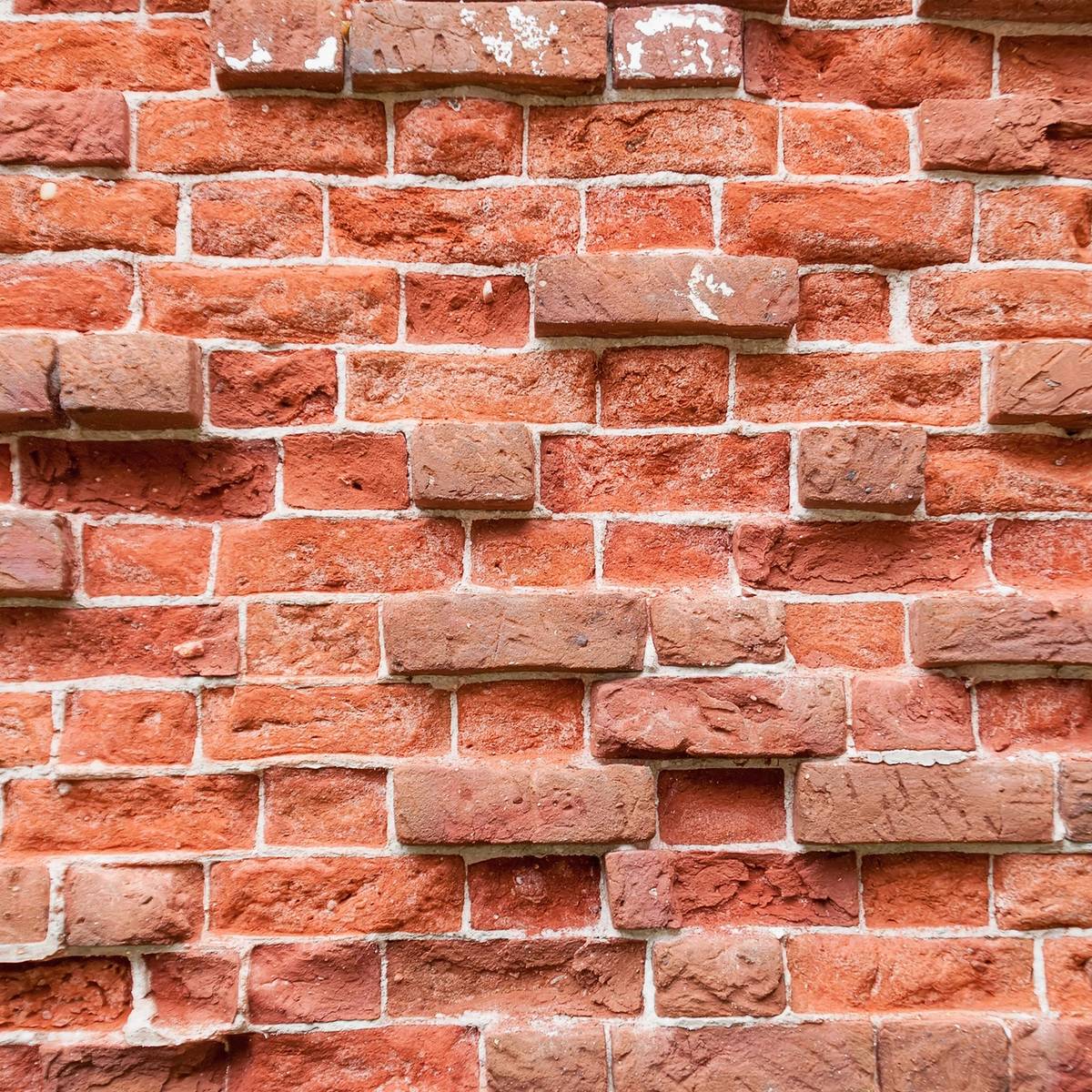
quality control reports
Quality control (QC) reports in construction are essential for ensuring that a project meets the required standards, specifications, and regulations. They document compliance with quality requirements and help track issues that arise during the construction process. Here are some key types of quality control reports typically required in a construction project

1.Inspection Reports
Daily Inspection Reports: Document the results of daily inspections, noting work completed and whether it meets the specified standards.
Material Inspection Reports: Focus on the quality of materials delivered on-site, ensuring they meet specifications before being used.
Structural Inspection Reports: Verify that the structural components (like foundations, beams, and columns) are in accordance with design standards and approved drawings.
Mechanical, Electrical, and Plumbing (MEP) Inspection Reports: Ensure that the installation of mechanical, electrical, and plumbing systems meets safety codes and design specifications.
2. Test Reports
Soil Testing Reports: Ensure the suitability of soil for foundations, compaction, and other load-bearing requirements.
Concrete Testing Reports: Document results from slump tests, compressive strength tests, and curing methods to ensure the concrete meets quality standards.
Steel Testing Reports: Cover tensile strength, bending, and welding tests on reinforcement and structural steel.
Asphalt Testing Reports: Focus on the quality of asphalt mixes for roadworks and pavements.
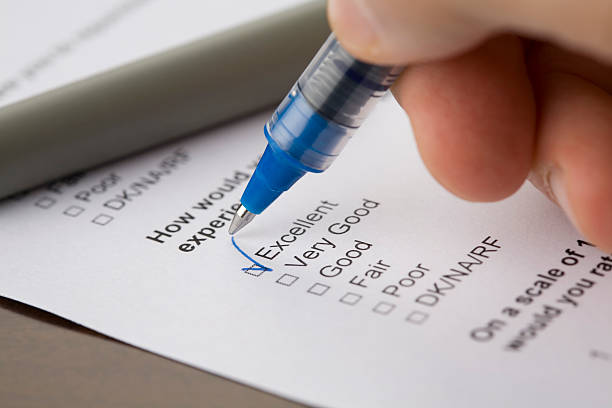
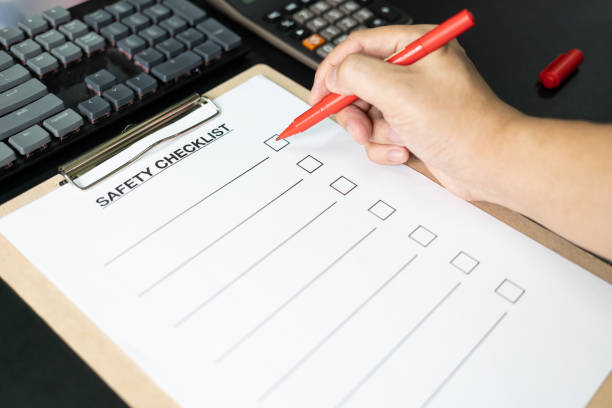
3. Non-Compliance Reports (NCR)
These reports document when a product, material, or work does not meet the project specifications, design, or regulatory standards. It helps in identifying areas that need corrective action.
4. Workmanship Inspection Reports
On-Site Workmanship Quality Reports: Evaluate the quality of construction work (e.g., brickwork, plastering, painting) and compare it to standards specified in project documentation.
Finishing Reports: Document the quality of final finishes, such as tiles, paints, and fixtures.
5. Equipment Calibration Reports
Ensure that all testing and measuring equipment used on the project (e.g., for concrete tests or steel measurements) is properly calibrated to industry standards.
6. Safety and Compliance Reports
These reports ensure that all safety measures, protocols, and procedures are in place and followed according to legal and regulatory requirements. It may also involve checking the quality of safety equipment like scaffolding.
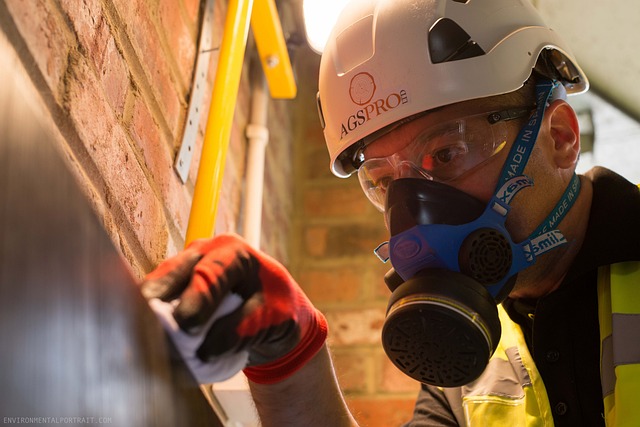
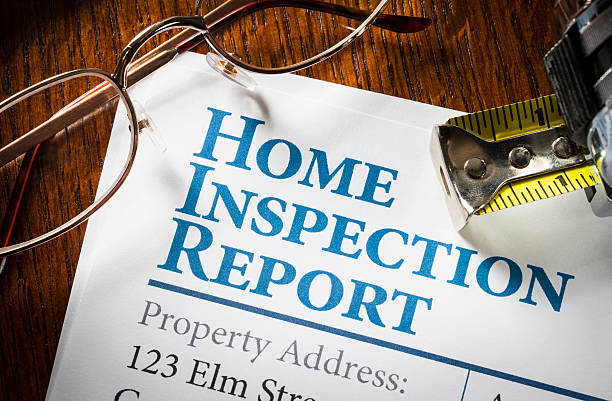
7. Punch List Reports
These are final inspection reports that list any remaining defects or incomplete items before the project handover. It documents quality-related tasks that need to be rectified to meet project specifications.
8. Environmental Impact Reports
In projects that require it, QC reports on environmental compliance can ensure the project adheres to environmental regulations, such as proper waste management, air quality, and water use.
9. Third-Party Quality Audit Reports
External audits by third-party agencies, sometimes required for high-stakes projects, offer an independent assessment of the quality of the project.
10. Handover and Final Acceptance Reports
These reports ensure that the completed project has met all contractual, regulatory, and quality standards, documenting a formal transfer of responsibility from the contractor to the client.
